
Flat Lapping and Polishing
Lapping and polishing are processes of building parts, similar to the five best known as turning, fresamento, drilling, grinding and conformation. Like the other processes, the stoning and polishing cut chips, except that in this case, microscopic and with a very low removal rate.
The difference between stoning and polishing is the surface that was generated by a stoning shows a matte surface, that does not reflect the light with micro abrasive risks made in chaotic directions.
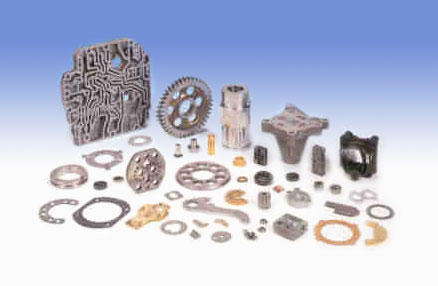
These tiny risks, cannot be confused with other deeper, caused by abrasive fluid contamination or other causes.
This is done for one reason: the generation of a surface capable of reflecting light. The need of this quality on a surface, pode ser criada para verificação da planicidade por interferência da luz, or to give best appearance in a play, to give the product a function as in the case of mirrors, or to decrease the friction coefficient of the surface.
No polishing improves the condition of surface seals. In a general way, polishing always comes after a cutting operation. The fundamental difference between cutting and polishing in terms of process, is that the stoning (lap in english -> loose abrasive particles) the abrasive elements are loose in the leads, While polishing, the abrasive elements are stuck on a.
The polishing operation, removes much less material than the cutting operation and is much slower. Lapping and polishing operations, can be used to generate roughness below 0,4 microns. Probably, in most cases, the reason for the rough is to generate a flat surface in a play. The process for measuring flatness is based on light interference, where the lower value is the band of light. A light band measures 0,2933 microns, based on monochromatic yellow light of Helium.
The stoning can generate flat surfaces within a band of light or less. There is no other process capable of generating a flat surface with this precision. To measure planicidades smaller than a band of light, you need an interferometer, which is capable of measuring flatness and roughness in the range of 0,0001 microm. Below, some examples of pieces that are cut.